Turbocharging sets the stage for a deep dive into the fascinating world of engine enhancement. This technology dramatically boosts power and performance, transforming how vehicles operate. From passenger cars to heavy-duty trucks, turbocharging is a crucial component in modern engines. This comprehensive exploration will unveil the intricate mechanics behind this powerful technology.
This detailed analysis will cover everything from the basic principles of turbocharging to its diverse applications across various industries. We’ll delve into different turbocharger types, their performance characteristics, and the crucial role they play in optimizing fuel efficiency and emissions. Maintenance and troubleshooting procedures will also be covered, ensuring a thorough understanding of this sophisticated system.
Introduction to Turbocharging
Turbocharging is a technology used to enhance the power output of combustion engines, particularly internal combustion engines (ICE). It achieves this by forcing more air into the engine’s cylinders, enabling the combustion process to produce more power and torque. This increased airflow directly translates to improved performance characteristics, including acceleration and top speed.The fundamental principle behind turbocharging relies on the kinetic energy of exhaust gases to drive a turbine, which in turn spins a compressor.
This compressor forces more air into the engine’s intake manifold, resulting in a denser air-fuel mixture. This denser mixture leads to more complete combustion, generating higher power outputs compared to naturally aspirated engines.
Historical Development of Turbocharging Technology
Early turbocharging applications emerged in the mid-20th century, primarily in diesel engines. The initial focus was on enhancing the efficiency of diesel engines, which often required high compression ratios. Later, advancements in turbine design and materials allowed for the application of turbocharging in gasoline engines, initially used for high-performance vehicles. The significant progress in turbocharging technology over the past few decades has led to its widespread adoption across a broad spectrum of vehicles, from passenger cars to trucks and even some racing applications.
Applications of Turbocharging Across Vehicle Types
Turbocharging has found widespread adoption across various vehicle types due to its ability to boost power output and efficiency. Passenger cars benefit from enhanced acceleration and responsiveness, while trucks utilize turbocharging for improved hauling capacity and fuel efficiency. Furthermore, high-performance vehicles frequently incorporate turbochargers to maximize engine power for track use.
Turbocharger Components and Functions
A turbocharger is a relatively simple yet sophisticated mechanism. It comprises several key components, each with a specific function.
Component | Function |
---|---|
Turbine | The turbine is driven by the high-velocity exhaust gases from the engine. Its function is to convert the kinetic energy of these exhaust gases into rotational energy, spinning the turbine shaft. |
Compressor | The compressor is connected to the turbine shaft. Its function is to compress the incoming air, increasing its density and pressure. This compressed air is then forced into the engine’s intake manifold. |
Turbine Housing | The turbine housing surrounds the turbine, directing the exhaust gases towards the turbine blades for efficient energy extraction. |
Compressor Housing | The compressor housing surrounds the compressor, directing the compressed air into the intake manifold for efficient delivery. |
Shaft | The shaft connects the turbine and compressor, transmitting the rotational energy from the turbine to the compressor. |
A typical turbocharger setup involves a turbine, a compressor, and a housing for both, all connected by a shaft. The high-velocity exhaust gases from the engine spin the turbine, which in turn spins the compressor. This compressed air is then delivered to the engine’s intake system.
Turbocharger Types and Configurations

Turbochargers are crucial components in boosting engine performance. They force more air into the combustion chamber, increasing the power output of internal combustion engines. Understanding the different types of turbochargers and their configurations is essential for selecting the optimal setup for a specific application.Turbocharger designs vary significantly, impacting their performance characteristics and suitability for different engines. This section delves into the different types, configurations, and their effects on engine efficiency.
Centrifugal Turbochargers
Centrifugal turbochargers utilize a centrifugal impeller to compress the incoming air. The air is accelerated as it moves radially outward from the impeller, increasing its pressure. This design is typically less complex and more affordable compared to axial turbochargers.
- Advantages: Centrifugal turbochargers are generally simpler in design, leading to lower manufacturing costs. They are also known for their relatively robust construction, making them suitable for high-stress applications.
- Disadvantages: They often exhibit lower efficiency compared to axial turbochargers, particularly at low engine speeds. Their relatively high pressure ratio can result in a more pronounced lag effect.
Axial Turbochargers
Axial turbochargers employ an axial impeller to compress the incoming air. The air flows axially through the impeller, resulting in a more gradual pressure increase. This design is generally more efficient, especially at lower speeds.
- Advantages: Axial turbochargers are highly efficient, especially at lower speeds, translating to better fuel economy and lower emissions. They typically exhibit a smoother response than centrifugal designs.
- Disadvantages: Axial turbochargers are more complex in design, leading to higher manufacturing costs. Their intricate components may be more prone to failure if not maintained correctly.
Turbocharger Configurations
Various configurations exist for turbochargers, each with specific implications for performance. These include single-scroll, twin-scroll, and V-band configurations. The choice of configuration often depends on the engine’s design and desired performance characteristics.
- Single-scroll turbochargers: A single exhaust manifold directs exhaust gases to a single turbine wheel. This design is relatively simple and cost-effective. However, it may lead to uneven exhaust gas flow, potentially impacting performance, particularly under variable load conditions.
- Twin-scroll turbochargers: Two separate exhaust manifolds direct exhaust gases to individual turbine wheels. This configuration improves exhaust gas flow and turbine efficiency, leading to a faster and more responsive turbocharger response, especially under partial load conditions.
- V-band turbochargers: This configuration utilizes a variable geometry turbine housing. This feature enables the turbine to adapt to different exhaust gas flows and engine speeds, leading to optimized performance across a broader range of operating conditions. This configuration often results in better throttle response and efficiency.
Turbocharger Geometry and Efficiency
Turbocharger geometry plays a crucial role in determining the efficiency of the turbocharger. The design of the turbine and compressor impellers significantly impacts the air flow, affecting pressure ratio and overall performance.
- Compressor Geometry: The compressor impeller shape and blade angle affect the pressure ratio achieved by the turbocharger. Optimizing these factors is essential for maximum air compression.
- Turbine Geometry: The turbine wheel shape and blade angle influence the turbine’s ability to extract energy from the exhaust gases. Optimizing these factors maximizes power recovery.
Factors Influencing Turbocharger Selection
Selecting the appropriate turbocharger for a specific application involves considering various factors. Engine type, power output requirements, and desired performance characteristics all play a role in the decision-making process.
- Engine Type: Different engine types, such as gasoline, diesel, and hybrid, have distinct requirements for turbocharger performance. For instance, diesel engines often require higher pressure ratios than gasoline engines.
- Desired Performance: The desired performance characteristics, including responsiveness, power output, and fuel efficiency, significantly influence the choice of turbocharger.
- Cost: Manufacturing cost is an important factor, especially in high-volume applications. The trade-off between performance and cost often influences the final selection.
Turbocharging Mechanisms and Processes
Turbocharging significantly enhances engine performance by forcing more air into the combustion chamber. This increased air supply allows for greater fuel combustion, resulting in higher power output and torque. Understanding the intricate interplay between the turbocharger and the engine is crucial for appreciating its effectiveness.The turbocharger, a rotary device, utilizes the exhaust gases’ energy to drive its turbine wheel.
This rotational energy is then transferred to a compressor wheel, compressing the incoming intake air. The compressed air, now denser, fuels more efficient combustion within the engine cylinders, ultimately boosting power output.
Exhaust Gas Pressure and Turbocharger Speed
The relationship between exhaust gas pressure and turbocharger speed is directly proportional. Higher exhaust gas pressure translates to a faster turbine speed, driving the compressor wheel at a higher rate. This increased rotational speed of the compressor results in a greater volume of compressed air delivered to the engine. Conversely, lower exhaust gas pressure leads to a slower turbine speed and reduced compressed air delivery.
This dynamic interplay is essential for optimal turbocharger performance. Engine load and RPM significantly influence exhaust gas pressure and consequently, turbocharger speed.
Turbocharger Boost Pressure Control
Wastegates are crucial components for regulating turbocharger boost pressure. They are essentially valves that divert exhaust gases away from the turbine when the boost pressure exceeds a predetermined level. This prevents the turbocharger from spinning at excessively high speeds, potentially damaging the engine or reducing efficiency. Wastegates are designed to open and close automatically based on the pressure difference.
The precise control of boost pressure ensures the engine operates within its optimal performance range. A well-tuned wastegate system provides a smooth and controlled power delivery.
Operational Cycle of a Turbocharger
The turbocharger’s operational cycle involves a continuous loop of exhaust gas utilization and intake air compression. Exhaust gases from the engine’s cylinders flow through the turbine housing, driving the turbine wheel. The rotation of the turbine is immediately transferred to the compressor wheel. The compressor then compresses the intake air, increasing its density. This compressed air is subsequently directed into the engine’s intake manifold, enriching the combustion process.
The compressed air increases the pressure in the engine’s cylinders, resulting in higher power output. This cyclical process repeats as long as the engine is running. The turbocharger’s efficiency relies on a well-maintained system and consistent airflow.
Performance Impacts of Turbocharging
Turbocharging significantly alters an engine’s performance characteristics, impacting power output, fuel efficiency, emissions, and overall responsiveness. This enhancement, achieved through forced induction, dramatically improves the engine’s ability to deliver power, though it also introduces certain limitations that must be considered. Understanding these effects is crucial for evaluating the suitability of turbocharging for various applications.The positive effects of turbocharging often outweigh the drawbacks, making it a popular choice for automotive and industrial applications.
This enhancement leads to notable increases in engine performance, though careful consideration of fuel economy and emissions is essential.
Positive Effects on Power and Torque
Turbocharging dramatically boosts engine power and torque across a wider range of engine speeds. The forced induction of air into the engine cylinders increases the density of the air-fuel mixture, leading to a significant increase in the power output of the engine. This results in improved acceleration and higher top speeds. For example, a turbocharged four-cylinder engine can often achieve power outputs comparable to a naturally aspirated six-cylinder engine, while maintaining a more compact design.
Increased torque is also a common outcome, providing a noticeable improvement in low-end performance.
Impact on Fuel Economy and Emissions
Turbocharging’s impact on fuel economy is complex and application-dependent. While turbocharging can lead to higher power output, it can also potentially reduce fuel economy in some situations, especially if not optimized properly. The improved fuel efficiency is directly related to the precise calibration of the engine management system. Modern turbocharged engines, equipped with advanced variable geometry turbochargers and precise fuel injection systems, often achieve comparable or even better fuel economy than naturally aspirated engines, especially under dynamic driving conditions.
However, the initial cost of the components and the need for careful tuning to optimize performance are factors to consider. In terms of emissions, turbocharging, when combined with advanced exhaust aftertreatment systems, can help reduce emissions compared to older naturally aspirated engines. However, the potential for increased emissions from unoptimized systems needs to be considered. Proper engine calibration and aftertreatment systems are vital to mitigate these potential issues.
Comparison with Naturally Aspirated Engines
Naturally aspirated engines rely solely on atmospheric pressure to draw air into the cylinders, while turbocharged engines use a turbocharger to force air into the cylinders. This difference in design results in distinct performance characteristics. Turbocharged engines typically deliver higher horsepower and torque at lower engine speeds, resulting in quicker acceleration and improved responsiveness. However, naturally aspirated engines often have a smoother, more linear power delivery, particularly at lower RPMs.
The choice between a turbocharged and naturally aspirated engine depends on the specific needs and priorities of the application. For example, in high-performance vehicles, the advantages of turbocharging often outweigh the disadvantages. In some applications, the superior fuel economy and lower emissions of naturally aspirated engines are desirable.
Effect on Engine Responsiveness and Acceleration
Turbocharged engines are renowned for their immediate and forceful responsiveness, often referred to as “turbo lag.” This is the delay experienced when accelerating from low speeds. Modern turbochargers and engine management systems minimize turbo lag by employing variable geometry turbochargers and sophisticated control algorithms. This minimizes the time it takes for the turbocharger to spool up, resulting in a smooth and responsive acceleration experience.
Advanced turbochargers, like those with variable turbine geometry, react more quickly to changes in engine load, resulting in improved acceleration.
Potential Limitations and Drawbacks
Turbocharging, while offering numerous benefits, does have potential limitations. One significant concern is the potential for increased complexity in the engine design and the increased cost of components. Turbochargers can require more maintenance and can be susceptible to damage if not properly maintained. The increased complexity of the system can also result in higher repair costs compared to naturally aspirated engines.
Another potential drawback is the risk of premature engine wear and tear under high-performance conditions, as the added pressure can place increased stress on engine components. Engine tuning and maintenance play a critical role in minimizing these potential drawbacks.
Turbocharging in Different Applications
Turbocharging significantly enhances engine performance across a wide spectrum of applications. Its ability to increase power output and efficiency makes it a valuable technology in various industries, from passenger vehicles to heavy-duty machinery. The specific design and configuration of turbochargers are often tailored to the unique demands of each application.Turbocharging’s versatility extends beyond simple performance gains. It plays a crucial role in meeting emission standards and improving fuel economy in numerous industries.
The adaptation of turbocharging to different applications involves careful consideration of factors like engine size, operating conditions, and desired power output.
Turbocharging in Passenger Cars
Turbocharging has become commonplace in passenger vehicles. Its compact design and ability to deliver significant power gains in smaller engines make it an attractive choice for manufacturers. This contributes to increased fuel efficiency and enhanced performance without sacrificing interior space or vehicle weight. The responsiveness and torque output provided by turbochargers are especially appealing in smaller displacement engines, enabling a more enjoyable driving experience.
Turbocharging in Trucks and Heavy-Duty Vehicles
In the realm of heavy-duty vehicles, turbocharging is indispensable. The high torque output and power density offered by turbochargers are essential for the demanding tasks these vehicles perform. Trucks, buses, and other heavy-duty vehicles often operate under constant load, making the consistent power delivery of a turbocharger crucial for optimal performance. Larger, more robust turbochargers are frequently employed in these applications to withstand the higher pressures and temperatures associated with heavy-duty operation.
Turbocharging in Marine Engines
Turbocharging marine engines has gained traction, particularly in applications like large vessels. The high power output and fuel efficiency improvements offered by turbochargers are significant benefits for marine applications. This allows for enhanced speed and maneuverability while minimizing fuel consumption, contributing to cost savings and environmental sustainability. The robust design and ability to withstand harsh marine environments are important factors in the selection of turbochargers for this application.
Turbocharging in Industrial Machinery
Turbocharging is increasingly used in various industrial applications. The ability to boost engine output while maintaining efficiency is crucial in tasks involving heavy loads and prolonged operation. From generators to compressors, turbochargers are enabling improved performance in a range of industrial machinery. The specific turbocharger configuration is often selected based on the unique operating parameters and power demands of each application.
Comparison of Turbocharger Applications
Application | Key Considerations | Typical Characteristics |
---|---|---|
Passenger Cars | Compact size, fuel efficiency, responsiveness | Smaller, lightweight turbochargers, optimized for low-to-medium pressure ratios |
Trucks and Heavy-Duty Vehicles | High torque, robustness, high-pressure operation | Larger, more robust turbochargers, capable of handling high pressures and temperatures |
Marine Engines | Robustness, durability, harsh operating conditions | High-pressure, high-temperature capability, often with specialized sealing and cooling systems |
Industrial Machinery | Specific power demands, operational longevity | Customized configurations to meet specific needs, potential for high-temperature and high-pressure operation |
Turbocharger Maintenance and Troubleshooting
Proper turbocharger maintenance is crucial for optimal engine performance, longevity, and safety. Neglecting maintenance can lead to significant issues, including decreased power output, increased fuel consumption, and potential engine damage. A well-maintained turbocharger operates efficiently and reliably, extending its lifespan and minimizing the risk of costly repairs.Regular inspection and servicing are vital for preventing premature wear and tear.
Troubleshooting any emerging problems promptly allows for timely repairs, avoiding escalation into more extensive and expensive issues. This section details the importance of maintenance, common problems, troubleshooting steps, and diagnostic techniques.
Importance of Regular Turbocharger Maintenance
Regular turbocharger maintenance encompasses various tasks, including visual inspections, lubrication checks, and component evaluations. This proactive approach significantly reduces the likelihood of major failures. By adhering to a scheduled maintenance routine, owners can proactively address potential issues before they escalate into costly repairs. Proper maintenance ensures consistent performance, maximizing the turbocharger’s lifespan.
Common Turbocharger Problems and Their Causes
Several issues can affect turbocharger performance. One prevalent problem is bearing failure. This often results from inadequate lubrication, leading to friction and subsequent damage. Another frequent problem is shaft wear, caused by excessive friction and lack of lubrication. Furthermore, issues like leaking seals or worn compressor/turbine vanes can arise due to improper installation, material degradation, or prolonged use.
Troubleshooting Steps for Turbocharger Issues
A systematic approach to troubleshooting is essential. Initial steps involve a visual inspection for leaks, unusual noises, or visible damage. Next, a thorough assessment of the lubrication system is crucial. Checking oil pressure and flow is critical. Furthermore, monitoring air intake pressure and exhaust gas temperature is essential.
These diagnostic steps often reveal the root cause of the problem.
Techniques for Diagnosing Turbocharger Malfunctions
Accurate diagnosis requires specialized tools and expertise. A pressure gauge is essential for checking compressor and turbine pressures. An exhaust gas analyzer can provide insights into exhaust gas composition, indicating potential problems. Sophisticated diagnostic software is often used to analyze engine parameters, providing further insights into turbocharger performance. Experienced technicians utilize their knowledge of turbocharger operation to interpret diagnostic data and pinpoint the source of malfunctions.
Typical Turbocharger Maintenance Schedules
| Maintenance Task | Frequency | Description ||—|—|—|| Visual Inspection | Weekly | Check for leaks, unusual noises, or damage. || Lubrication Check | Monthly | Verify oil levels and quality. || Component Evaluation | Quarterly | Assess wear and tear on critical components. || Pressure Testing | Annually | Measure compressor and turbine pressures to ensure optimal performance. || Full Service | Yearly | Comprehensive service including cleaning, lubrication, and component replacement if necessary.
|
Turbocharger Materials and Manufacturing
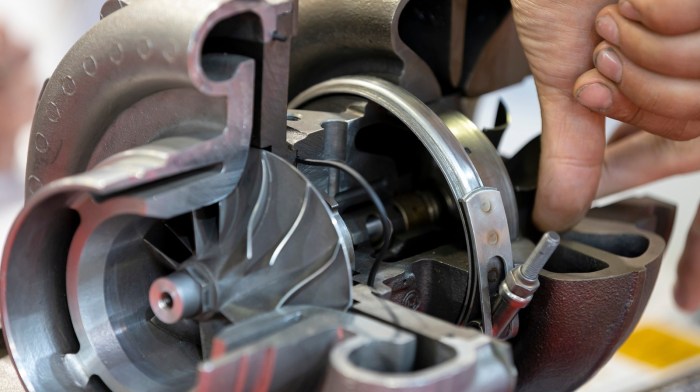
Turbochargers, crucial components in enhancing engine performance, are meticulously crafted from a variety of materials. The selection of these materials is directly tied to the demanding operational conditions they face, including extreme temperatures, pressures, and vibrations. The manufacturing processes employed are equally important, guaranteeing the desired performance and longevity of these vital components.
Materials Used in Turbocharger Construction, Turbocharging
The materials chosen for turbocharger components significantly impact their durability, efficiency, and overall performance. Critical components, such as the turbine wheel, compressor wheel, and housing, are subjected to high temperatures, stresses, and corrosive environments. This necessitates the use of materials with specific properties.
- Turbine and Compressor Wheels: High-strength alloys of nickel-based superalloys, or even titanium alloys, are often used for turbine and compressor wheels. These alloys exhibit exceptional strength and resistance to high temperatures, preventing deformation and maintaining precise aerodynamic shapes under extreme operating conditions. Specific examples include Inconel, Nimonic, and Waspaloy. The selection depends on the targeted operating temperature and required mechanical strength.
Turbocharging systems are super-efficient, but they require a significant amount of power. This directly relates to the need for readily available and reliable EV charging stations, like those found at EV charging stations , to support the growing adoption of electric vehicles. Ultimately, the future of turbocharging will likely rely on this type of infrastructure.
- Housing Materials: Cast iron, or more advanced materials like high-temperature alloys, are commonly employed for the turbocharger housing. These materials provide the necessary structural integrity to withstand the pressure and thermal gradients experienced during operation. Modern designs often utilize composite materials for improved strength-to-weight ratios.
- Shaft Materials: High-strength steel alloys are used for the turbocharger shaft, which transmits rotational power between the turbine and compressor. These materials must withstand the immense stresses and vibrations generated during operation. Specific steel grades, like hardened tool steels, are frequently chosen for their exceptional durability.
Manufacturing Processes
The manufacturing processes involved in creating turbochargers are highly sophisticated and precise. These procedures ensure the creation of components with precise tolerances, ensuring smooth operation and optimal performance.
- Casting: The production of larger components like housings frequently involves casting processes. These methods allow for the creation of complex shapes and ensure uniformity in the material properties. Different casting techniques, such as investment casting or die casting, are used based on the complexity and size of the component.
- Forging: For components requiring high strength and precise dimensions, such as turbine and compressor wheels, forging is often employed. This process involves shaping the material under intense pressure, resulting in a denser and more homogeneous structure, enhancing the mechanical properties of the components.
- Machining: After casting or forging, machining processes, including grinding, turning, and milling, are crucial for achieving the required tolerances and surface finishes on the components. These procedures ensure the precise fit between parts and the smooth operation of the turbocharger.
- Heat Treatment: To improve the mechanical properties of the materials, heat treatment procedures are frequently implemented. These procedures can include annealing, quenching, and tempering to alter the material’s microstructure and achieve the desired strength, hardness, and toughness. This process is vital to ensure the material’s resistance to failure under operational stress.
Quality Control in Turbocharger Production
Ensuring the quality of turbocharger components is paramount. Strict quality control measures are implemented throughout the manufacturing process to minimize defects and guarantee reliable performance.
- Dimensional Inspection: Rigorous dimensional inspections are carried out to verify that components meet the required tolerances. This involves utilizing specialized measuring instruments to assess dimensions, ensuring that parts fit together correctly.
- Material Testing: Testing the material properties, including tensile strength, hardness, and fatigue resistance, is crucial to guarantee the component’s suitability for the intended application. This ensures the material’s ability to withstand the stresses and temperatures during operation.
- Performance Testing: Thorough performance testing of assembled turbochargers is vital to verify their operational efficiency, flow rates, and other critical parameters. These tests assess the performance characteristics and functionality of the complete unit.
Factors Influencing Turbocharger Durability
Several factors significantly influence the durability of turbochargers. Understanding these factors is crucial for optimizing the design and manufacturing processes.
- Material Selection: The choice of materials plays a pivotal role in determining the turbocharger’s ability to withstand the harsh operational conditions. High-temperature alloys, for example, enhance the durability of turbine and compressor components.
- Manufacturing Process: The precision and quality of the manufacturing processes significantly affect the durability of the turbocharger. Precise machining and heat treatments, for instance, enhance the structural integrity of components.
- Operational Conditions: The operating conditions, including temperature, pressure, and vibrations, are crucial determinants of turbocharger longevity. Operating within specified parameters is essential for maximizing the component’s life.
Types of Bearings Used in Turbochargers
Various types of bearings are employed in turbochargers to support the rotating shaft. These bearings are critical for ensuring smooth rotation and reducing friction.
- Ball Bearings: Used in various turbocharger applications, ball bearings are known for their high load-carrying capacity. Their relatively simple design contributes to their affordability and widespread use in many applications.
- Roller Bearings: Used in some high-performance turbochargers, roller bearings offer a higher load capacity compared to ball bearings and are well-suited for applications requiring high speeds and significant loads.
- Ceramic Bearings: Ceramic bearings exhibit excellent performance at high temperatures and can operate at higher speeds than other bearing types. They are often utilized in demanding applications, where temperature resistance and reduced friction are crucial.
Turbocharging and Emissions Control
Turbocharging, while boosting engine performance, can introduce complexities in managing emissions. Optimizing turbocharged engine designs and incorporating advanced emission control technologies are crucial for meeting increasingly stringent environmental regulations. This section explores the impact of turbocharging on emissions, mitigation strategies, and the role of catalytic converters and advanced technologies in achieving compliance.The heightened combustion pressures and temperatures in turbocharged engines can lead to the formation of more pollutants compared to naturally aspirated engines.
However, careful engineering and the integration of emission control systems can significantly reduce these emissions to meet stringent environmental standards.
Impact of Turbocharging on Emissions
Turbocharging, by increasing the air intake, leads to higher combustion temperatures and pressures, which can increase the production of nitrogen oxides (NOx). Additionally, the increased fuel consumption in some turbocharged engines can also contribute to higher emissions of unburnt hydrocarbons (HC) and carbon monoxide (CO). These pollutants, if not properly managed, can contribute to smog formation and other air quality issues.
Turbocharging boosts engine performance, but the trade-offs in efficiency are significant. Considering the rise of hybrid and electric vehicles, like those detailed in the Hybrid vs electric comparison, it’s important to weigh the pros and cons of turbocharging against these alternative powertrains. Ultimately, turbocharging still plays a crucial role in many modern engine designs.
Strategies for Mitigating Emissions
Several strategies are employed to mitigate emissions from turbocharged engines. These include optimizing the engine’s design to minimize the formation of pollutants during combustion, using advanced combustion techniques such as stratified charge or homogeneous charge compression ignition (HCCI), and incorporating efficient exhaust aftertreatment systems. Careful tuning of the engine’s control system to manage the fuel-air mixture is also vital.
Role of Catalytic Converters
Catalytic converters are essential components in managing emissions from turbocharged engines. These devices use catalytic reactions to convert harmful pollutants like NOx, CO, and HC into less harmful substances such as nitrogen, carbon dioxide, and water vapor. Different catalytic converter designs exist, utilizing various precious metals like platinum, palladium, and rhodium, to facilitate these reactions. The effectiveness of a catalytic converter depends on its size, material composition, and operating temperature.
Advanced Emission Control Technologies
Advanced emission control technologies are constantly evolving to address the specific challenges of turbocharged engines. Selective catalytic reduction (SCR) systems, for instance, inject urea or ammonia into the exhaust stream to further reduce NOx emissions. Other technologies, like three-way catalytic converters and oxidation catalysts, effectively reduce HC and CO emissions. The adoption of these advanced technologies ensures that turbocharged vehicles comply with ever-tightening emission standards.
Regulations and Standards
Stringent regulations and standards govern emissions from turbocharged vehicles. These regulations vary across jurisdictions and evolve over time, reflecting advancements in emission control technologies and environmental concerns. Manufacturers must demonstrate compliance with these standards through rigorous testing and certification procedures. These standards often mandate specific emission limits for NOx, CO, HC, particulate matter, and other pollutants. Examples include the Euro emission standards and the U.S.
EPA regulations. These standards have driven the development and adoption of advanced emission control systems in turbocharged engines.
Future Trends in Turbocharging Technology
Turbocharging technology is constantly evolving, driven by the need for higher efficiency, reduced emissions, and improved performance in various applications. This evolution is not just incremental; it’s marked by a shift towards innovative designs and the integration of cutting-edge technologies. This section explores emerging trends, highlighting advancements in turbocharger design and their impact across different sectors.
Emerging Technologies in Turbocharger Design and Development
Modern turbocharger design is increasingly incorporating advanced materials, such as lightweight alloys and ceramics, to reduce mass and enhance efficiency. Computational fluid dynamics (CFD) plays a crucial role in optimizing the flow characteristics within the turbocharger components. These advancements aim to reduce friction, improve airflow, and ultimately boost overall performance.
Potential Future Advancements in Turbocharging Technology
Future turbocharging technology is likely to see the integration of more sophisticated control systems, allowing for dynamic adjustments in boost pressure based on real-time engine conditions. This adaptive control, combined with advanced materials, could further enhance efficiency and reduce emissions. Moreover, the exploration of variable geometry turbochargers with more complex designs promises to further optimize performance across a broader range of operating conditions.
Role of Electric Motors in Hybrid and Electric Vehicles with Turbochargers
In hybrid and electric vehicles (HEVs/EVs), turbochargers are finding a unique role. Electric motor-driven turbochargers (EMTDs) offer significant advantages. They allow for more precise control of boost pressure, facilitating quicker responses and enhanced efficiency. Furthermore, EMTDs can enable electric-only driving modes, potentially reducing friction and enhancing overall fuel economy in HEVs.
Examples of Turbocharger Designs that Enhance Efficiency
Several designs are emerging to boost efficiency. One example is the development of variable nozzle vanes (VNVs) that enable a more dynamic control of airflow. Another is the incorporation of advanced coatings on the compressor and turbine blades to reduce friction and improve heat transfer. Moreover, designs that optimize the flow path, reducing turbulence and pressure drops, are increasingly employed.
Role of Computational Fluid Dynamics in Turbocharger Design Optimization
Computational fluid dynamics (CFD) is revolutionizing turbocharger design. Sophisticated CFD models allow engineers to simulate airflow, heat transfer, and other critical parameters within the turbocharger. This enables them to identify potential areas for improvement and optimize the design before physical prototypes are built. This significantly reduces development time and costs, and enhances the efficiency and performance of the final product.
“CFD simulations provide a detailed understanding of the complex flow patterns within a turbocharger, allowing for precise adjustments to the design.”
CFD analysis enables detailed optimization of blade geometries, flow channels, and other critical aspects, leading to enhanced performance and reduced emissions.
Turbocharging and Fuel Efficiency
Turbocharging, while enhancing engine power, can significantly impact fuel efficiency. The relationship between turbocharging and fuel economy is complex, and understanding this interplay is crucial for optimizing performance and minimizing environmental impact. Factors like turbocharger size, design, and the engine management system all play critical roles in achieving this balance.Turbocharging can lead to improved fuel efficiency in certain scenarios, but this is not a guaranteed outcome.
The effectiveness depends on careful design and integration into the overall engine system. A well-engineered turbocharger system can deliver enhanced fuel economy, but a poorly designed or mismatched one can be detrimental to fuel efficiency.
Impact on Fuel Economy
Turbocharging can improve fuel efficiency in several ways. By increasing the density of air entering the combustion chamber, turbocharging can enhance combustion efficiency, meaning more power is generated with less fuel. However, the added complexity of the turbocharger system itself can sometimes lead to increased parasitic losses, potentially offsetting some of the gains in efficiency. This trade-off needs careful consideration during the design phase.
Comparison with Naturally Aspirated Engines
Naturally aspirated engines rely solely on atmospheric pressure to draw in air. Turbocharged engines, on the other hand, utilize a turbine to pressurize the intake air, enabling more complete combustion and higher power output. Generally, turbocharged engines can achieve comparable or slightly better fuel economy at higher loads, but fuel efficiency at lower loads can be affected. The specific fuel economy difference will vary depending on engine design, driving conditions, and operating parameters.
Turbocharging Strategies for Optimized Fuel Efficiency
Several strategies can optimize fuel efficiency with turbocharging. One strategy is variable turbine geometry (VTG), where the turbine’s geometry adjusts to optimize airflow at different engine speeds and loads. This enables the turbocharger to respond efficiently across a broader range of engine operating conditions. Another strategy is to employ smaller turbochargers, which can reduce parasitic losses, leading to better fuel economy at lower speeds.
Influence of Turbocharger Size and Design
The size and design of the turbocharger are critical to fuel economy. Larger turbochargers generally offer higher boost pressures at higher engine speeds, but can lead to increased parasitic losses and reduced fuel efficiency at lower speeds. Conversely, smaller turbochargers may provide insufficient boost at higher speeds. An optimal design will strike a balance between power output and fuel economy across the entire engine operating range.
Engine Management System Optimization
Engine management systems play a crucial role in optimizing fuel efficiency with turbocharging. Sophisticated control algorithms can precisely adjust fuel delivery, ignition timing, and boost pressure based on real-time engine conditions. This allows the engine to operate at the most efficient point possible, maximizing fuel economy without compromising performance. Modern systems utilize sensors and actuators to dynamically control the turbocharger and optimize its function within the engine’s operating parameters.
Outcome Summary: Turbocharging
In conclusion, turbocharging has revolutionized engine design, offering significant performance gains and efficiency improvements. Its versatility extends across various vehicle types, from passenger cars to industrial machinery. While challenges exist, continuous advancements in technology promise even greater performance and sustainability in the future. We’ve explored the fundamental principles, applications, and intricacies of turbocharging, providing a thorough understanding of this crucial technology.
Clarifying Questions
What are the common causes of turbocharger failure?
Common causes include insufficient lubrication, excessive heat, and damage from debris in the exhaust stream. Over time, the seals and bearings can wear out, leading to leaks or malfunctions.
How does turbocharging affect fuel economy?
Turbocharging can improve fuel economy by increasing engine efficiency, but this depends on the specific design and operating conditions. A well-designed turbocharger system can often result in improved fuel efficiency compared to a naturally aspirated engine, especially under higher load conditions.
What are the different types of turbocharger bearings?
Common types include ball bearings, roller bearings, and journal bearings. The choice of bearing type often depends on the specific application and desired performance characteristics.