Engine troubleshooting, a crucial skill for any vehicle owner, covers a wide range of potential problems. From simple issues like low coolant to complex problems involving the electrical system, this guide provides a comprehensive overview of diagnostic methods and repair procedures.
This guide will walk you through identifying common engine problems, troubleshooting techniques for various systems, and specific considerations for different engine types. Whether you’re a seasoned mechanic or a novice, this resource will equip you with the knowledge and steps to effectively diagnose and resolve issues with your engine.
Identifying Common Engine Problems
Engine malfunctions can manifest in various ways, from subtle changes in performance to dramatic failures. Understanding the common symptoms and their potential causes is crucial for timely diagnosis and repair, preventing further damage and costly repairs. Early detection often leads to more affordable and less extensive fixes.A well-maintained engine typically operates smoothly and efficiently. However, various factors, such as wear and tear, fuel quality, or environmental conditions, can lead to performance issues.
This section details common engine problems, categorized by their associated symptoms, to aid in their identification and diagnosis.
Loss of Power
Several factors can cause a loss of power in an engine. This symptom often requires a systematic approach to diagnosis. Insufficient fuel delivery, air intake restrictions, or problems with the ignition system are among the most frequent causes. Other possible culprits include worn-out components like the spark plugs, fuel injectors, or the air filter.
- Insufficient Fuel Delivery: A clogged fuel filter or a malfunctioning fuel pump can restrict fuel flow, leading to a noticeable drop in power. This often presents as a gradual decrease in performance rather than a sudden complete loss.
- Air Intake Restrictions: A clogged air filter or a problem with the intake manifold can reduce the amount of air reaching the engine. This can lead to a significant loss of power, especially under load.
- Ignition System Issues: Malfunctioning spark plugs, ignition coils, or a faulty distributor can disrupt the ignition process, leading to a drop in power. Symptoms might include rough idling, misfires, and a general lack of acceleration.
- Worn Components: Over time, components like spark plugs and fuel injectors can wear out. This wear can gradually decrease the engine’s performance and power output.
Unusual Noises
Unusual noises emanating from the engine can indicate various underlying issues. Pinpointing the specific sound and its location can help diagnose the problem. These sounds range from a grinding sound to a ticking or knocking sound.
- Knocking/Pounding Noise: A knocking sound, often described as a metallic clang, can indicate issues with worn-out bearings, pistons, or connecting rods. This is a serious problem that can lead to significant damage if not addressed promptly.
- Grinding Noise: A grinding noise is typically indicative of severe mechanical damage, such as a damaged camshaft, crankshaft, or timing chain/belt. This is a serious issue requiring immediate attention.
- Ticking Noise: A ticking sound, especially if it changes with engine speed, might suggest issues with the valve train or other components.
Overheating
Engine overheating is a significant issue that can lead to severe damage if not addressed promptly. A variety of factors can contribute to this problem, from a lack of coolant to a malfunctioning thermostat.
- Coolant Leaks: A leak in the cooling system will reduce the amount of coolant, causing the engine to overheat. Check for leaks around the radiator, hoses, and water pump.
- Faulty Thermostat: A faulty thermostat can fail to open or close properly, disrupting the engine’s temperature regulation. This will result in the engine operating at either an excessively high or low temperature.
- Clogged Radiator: A clogged radiator can hinder the flow of coolant, leading to reduced cooling efficiency and overheating.
Symptom Comparison Table
Symptom | Misfiring | Low Compression | Overheating |
---|---|---|---|
Loss of Power | Yes | Yes | No (but can cause loss of power in severe cases) |
Unusual Noises | Possible (rough running) | Possible (knocking) | Possible (pumping noise) |
Overheating | No | No | Yes |
Other Symptoms | Rough idle, misfires | Hard starting, difficulty accelerating | High temperature gauge, steam from the radiator |
Troubleshooting Techniques
Engine troubleshooting requires a systematic approach to identify and resolve issues efficiently. A methodical process, encompassing visual checks, listening for anomalies, and using diagnostic tools, is crucial for pinpointing the root cause of engine problems. This approach minimizes wasted time and resources, ultimately leading to a more effective repair.Effective troubleshooting goes beyond simply replacing parts. It involves understanding the interplay of components and identifying the specific problem area.
This often necessitates a combination of visual inspections, auditory assessments, and diagnostic tools to accurately diagnose the issue. Careful examination of fluid levels, component connections, and operational sounds are integral to this process.
Visual Inspections
Visual inspections are an initial, essential step in troubleshooting. Inspecting for obvious signs of damage, leaks, or unusual wear is vital. This involves checking belts, hoses, wires, and other visible components for signs of fraying, cracks, or leaks. A thorough visual inspection can reveal critical issues early in the process, preventing further damage or unnecessary diagnostic steps.
Auditory Assessments
Listening for unusual sounds during engine operation is a key part of troubleshooting. A variety of sounds, from knocking noises to grinding or hissing sounds, can indicate potential issues. Identifying these sounds can significantly narrow down the possibilities and guide the diagnostic process. For instance, a rhythmic ticking sound might point to a loose part, while a grinding sound may suggest a damaged bearing.
Using Diagnostic Tools
Modern diagnostic tools provide valuable data for troubleshooting engine problems. These tools can read engine codes, monitor sensor readings, and display various performance parameters. Tools like scanners and oscilloscopes can pinpoint specific sensor faults or wiring issues, leading to faster and more precise diagnoses. Data captured from these tools can be compared to manufacturer specifications for a more thorough analysis.
Methodical Troubleshooting
A methodical approach is essential for effective troubleshooting. A structured sequence of steps, from initial observations to detailed checks, ensures that no potential problem is overlooked. This involves documenting findings, testing hypotheses, and systematically evaluating possible causes. Skipping steps can lead to misdiagnosis and unnecessary repairs. The table below exemplifies a structured approach to troubleshooting misfiring.
Troubleshooting Misfiring
A misfiring engine can manifest in several ways, from rough idling to erratic acceleration. A structured approach to troubleshooting this problem is crucial.
Step | Action | Possible Results |
---|---|---|
1 | Visual Inspection (engine compartment) | Check for loose connections, damaged wires, or obvious leaks. |
2 | Check Spark Plugs | Examine for excessive wear, fouling, or broken electrodes. |
3 | Check Spark Plug Wires | Look for cracks, damage, or high resistance. |
4 | Check Fuel System | Ensure proper fuel pressure, fuel filter condition, and injectors are working correctly. |
5 | Verify Air Intake System | Assess for clogs, leaks, or restrictions in the intake. |
6 | Use Diagnostic Tools (if applicable) | Read codes for sensor faults or other system errors. |
Fuel System Troubleshooting
The fuel system is crucial for engine operation, delivering the proper fuel-air mixture to the combustion chambers. Malfunctions in this system can lead to a wide range of performance issues, from rough idling to complete engine failure. Understanding the fuel system components and their roles is key to effective troubleshooting.Fuel system problems often manifest as power loss, hesitation, stalling, or unusual noises.
A systematic approach to diagnosing these problems, focusing on fuel delivery, pressure, and injectors, is essential for efficient repair.
Fuel Delivery Issues
Diagnosing fuel delivery issues involves a methodical approach, beginning with a visual inspection for leaks and checking fuel pressure readings. Low fuel pressure can be caused by a faulty fuel pump or a clogged fuel filter. High pressure may indicate a problem with the pressure regulator. These issues can result in inadequate fuel delivery, leading to poor engine performance.
Role of Fuel System Components
The fuel system comprises several interconnected components, each playing a critical role in engine function. Fuel injectors precisely meter fuel into the combustion chamber, ensuring the correct fuel-air mixture. A clogged fuel filter restricts fuel flow, potentially causing engine misfires or stalling. The fuel pump, the heart of the system, provides the necessary pressure to deliver fuel to the injectors.
Diagnosing Fuel Leaks
Visual inspections are the first step in diagnosing fuel leaks. Look for wet spots or puddles around the fuel lines, fuel injectors, and the fuel pump. Use a leak detection spray (a non-flammable, non-toxic substance) to pinpoint the exact location of the leak. Listen for hissing sounds, particularly around fuel components. These methods can quickly identify fuel leaks and prevent potential safety hazards.
Fuel-Related Engine Problems: Causes
Fuel-related engine problems can stem from various causes, each with distinct characteristics. Clogged fuel filters restrict fuel flow, causing the engine to run poorly or stall. Faulty fuel injectors may deliver an inconsistent or incorrect fuel-air mixture, leading to misfires and reduced power. A weak or failing fuel pump may not produce sufficient pressure, leading to poor acceleration or stalling.
These factors often result in similar symptoms, making diagnosis challenging. For instance, a clogged filter and a weak fuel pump can both result in poor acceleration, but the underlying causes and solutions are different. A thorough examination of each component is essential for accurate diagnosis. Examples include fuel filter replacement for clogged filters, and fuel pump replacement for weak pumps.
Ignition System Troubleshooting
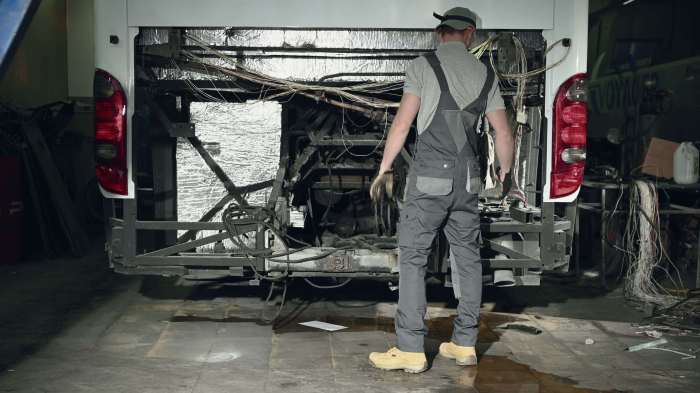
The ignition system is crucial for starting and running a vehicle. It ensures the engine receives the correct electrical signals to ignite the air-fuel mixture. Problems in this system can manifest as starting issues, rough idling, or complete engine failure. Understanding the components and their functions is key to diagnosing and fixing these problems effectively.
Spark Plug Function
Spark plugs are the critical components that ignite the compressed air-fuel mixture in the combustion chamber. They create a high-voltage spark across a gap, igniting the mixture. The condition of the spark plug significantly impacts engine performance. Proper spark plug gap, electrode condition, and material composition are essential for reliable ignition.
Spark Plug Testing
Visual inspection is a first step in evaluating spark plug condition. Look for signs of fouling, excessive wear, or damage. A visual inspection is a simple yet effective method to determine if the spark plug is in proper working condition. If there is a significant amount of carbon buildup or unusual wear, the spark plug may need replacement.
For a more in-depth assessment, use a spark plug tester. This tool will visually and electrically determine if the spark plug is operating properly. It also can identify any issues with the electrical conductivity.
Spark Coil Function
Spark coils, also known as ignition coils, step up the low voltage from the battery to the high voltage required for the spark plug to fire. They are responsible for transferring the energy from the battery to the spark plug, allowing for a high-voltage spark. Their role is crucial in the ignition process. A malfunctioning coil can lead to inconsistent or weak spark, impacting engine performance.
Distributor Function (If Applicable)
Distributors (often found in older vehicles) are components that time the spark to the appropriate cylinder. They direct the high-voltage current to the appropriate spark plug at the correct time during the engine cycle. This ensures that each cylinder receives the spark needed for efficient combustion. Modern vehicles often use electronic ignition systems that eliminate the need for a distributor.
Ignition System Troubleshooting Procedures
First, check the battery voltage. A low battery voltage can lead to weak spark. Next, inspect the wiring for any damage or corrosion. This is a crucial step in the diagnosis. Check for proper connections and continuity.
Verify the spark plug gap is within the manufacturer’s specifications. Using a spark tester to check spark plug function and the coil voltage output is essential. If a distributor is present, check its internal components for damage or wear.
Components and Potential Issues Table
Component | Potential Issues |
---|---|
Spark Plugs | Fouling, damaged electrodes, incorrect gap, improper heat range |
Spark Coils | Low voltage output, internal short circuits, damaged insulation |
Distributor (if applicable) | Internal component failure, damaged wiring, incorrect timing |
Wiring | Damage, corrosion, poor connections, loose terminals |
Ignition System Control Module (if applicable) | Malfunctioning module, incorrect signals, component failure |
Cooling System Troubleshooting
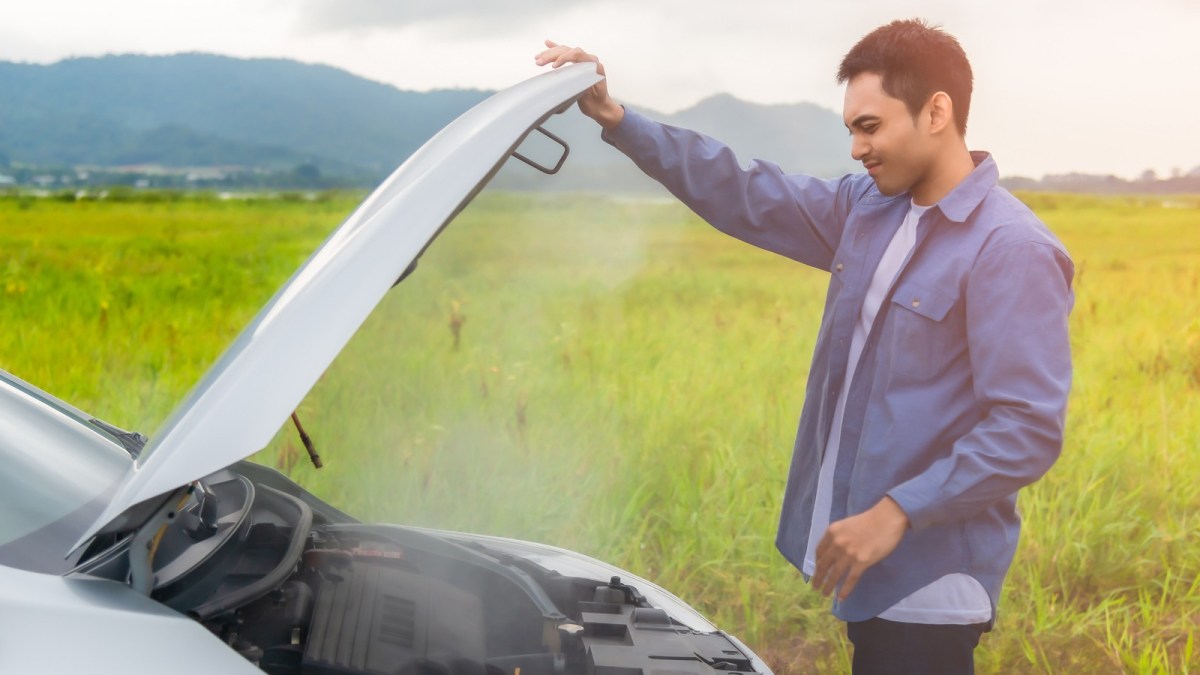
The cooling system is crucial for engine longevity and performance. It prevents overheating, which can lead to significant damage to engine components. Proper functioning of the cooling system ensures optimal operating temperatures, enabling efficient combustion and preventing thermal stress.The cooling system’s primary function is to circulate coolant through the engine’s various components. This coolant absorbs heat generated during combustion, carrying it away from the engine and dissipating it through the radiator.
A well-maintained cooling system is vital for maintaining engine temperature within the specified range, thus extending its lifespan.
Identifying Cooling System Leaks
Visual inspection is a fundamental step in identifying cooling system leaks. Look for wet spots on the engine, particularly around hoses, joints, and the radiator. Pay close attention to areas where coolant lines connect or where hoses bend. Check the ground beneath the engine for pooling or dripping coolant. If a leak is suspected, allow the engine to cool completely before inspecting it.
Testing Coolant System Pressure
Proper coolant system pressure is essential for efficient operation. A pressure test aids in identifying leaks and potential issues within the system. The procedure involves using a pressure gauge and appropriate tools to measure the pressure within the cooling system. The gauge should be connected to the cooling system according to the vehicle’s specifications. A significant drop in pressure over time indicates a leak.
Normal pressure readings vary based on the vehicle model and operating temperature.
Troubleshooting Overheating Issues
Overheating is a serious engine problem that can quickly lead to catastrophic failure. A number of factors can contribute to overheating, including leaks, insufficient coolant levels, air pockets, and a malfunctioning thermostat. A systematic approach to troubleshooting is crucial.
- Coolant Level Check: Ensure the coolant reservoir is full to the proper level. A low coolant level compromises the system’s ability to absorb heat, leading to overheating. Check the reservoir frequently and top it off as needed. Note the appropriate coolant level for your vehicle model.
- Thermostat Function: A faulty thermostat can prevent the coolant from circulating properly, leading to overheating. Verify the thermostat is functioning correctly. This is best performed with a specialized diagnostic tool or by consulting a qualified mechanic if you are unsure of the specific procedure for your vehicle.
- Radiator Inspection: A clogged radiator can hinder the dissipation of heat, leading to overheating. Inspect the radiator for blockages, and ensure the radiator fins are clean and unobstructed. A clean radiator ensures efficient heat dissipation.
- Fan Operation: Ensure the cooling fan is functioning properly. A malfunctioning fan can impede the cooling process. A visual inspection and a functional test will confirm if the fan is operating correctly. Observe the fan’s operation during various engine speeds to gauge its efficiency.
Electrical System Troubleshooting
The electrical system is the nervous system of a vehicle’s engine. It controls crucial functions like starting, running, and regulating various components. Proper functioning of the electrical system is paramount for reliable engine performance. Malfunctions can manifest in various ways, impacting the engine’s ability to operate correctly.The electrical system comprises a complex network of wires, components, and sensors that communicate and interact to control the engine’s operations.
This includes the battery, alternator, starter motor, ignition system, sensors (like oxygen sensors and temperature sensors), and various control units. Understanding the roles of these components and how they interconnect is crucial for effective troubleshooting.
Engine troubleshooting can be a real pain, but tackling it yourself with a bit of know-how and the right resources, like learning from DIY car repair guides, can make it much easier. A good understanding of basic car mechanics can significantly improve your ability to diagnose and fix engine problems. Ultimately, a solid understanding of engine troubleshooting is key to keeping your car running smoothly.
Electrical System Components and Functions
The electrical system’s core components play vital roles in engine operation. The battery provides the initial power needed to start the engine. The alternator charges the battery while the engine is running, ensuring a consistent power supply. The starter motor is activated by the electrical system to crank the engine, getting it to ignite. Sensors monitor various engine parameters and relay information to the control unit.
The control unit interprets the sensor data and adjusts the engine’s operation accordingly.
Engine troubleshooting can be tricky, but understanding the nuances of modern car designs, like those featured in the Best cars 2025 list, is key. Different models have varying complexities, demanding a thorough understanding of the specific systems and components. Ultimately, a solid grasp of the underlying mechanics is crucial for effective troubleshooting.
Common Electrical Problems
Numerous electrical issues can arise, affecting the engine’s performance. These problems range from simple loose connections to more complex issues with control modules. Common problems include faulty wiring, malfunctioning relays, damaged components (such as the alternator or starter motor), and issues with the control unit. Furthermore, poor battery condition, low voltage, or parasitic electrical drain can also lead to issues.
Testing and Diagnosing Electrical Components
A systematic approach to testing and diagnosing electrical components is essential. First, inspect all visible connections for corrosion, damage, or loose connections. Use a multimeter to verify voltage levels at key points in the system. This helps determine if the power is reaching the intended destination. Furthermore, test the operation of individual components, such as the starter motor and alternator.
If issues persist, consult the vehicle’s repair manual for specific diagnostic procedures. Proper tools and techniques are critical to avoid further damage.
Diagnostic Table
Fault | Symptoms | Possible Causes |
---|---|---|
Faulty Starter Motor | Engine does not crank, clicking sound, or weak cranking. | Worn starter motor components, damaged wiring, low battery voltage. |
Malfunctioning Alternator | Dim headlights, low battery voltage, warning lights illuminated, poor engine performance. | Damaged alternator belt, internal alternator problems, poor wiring. |
Wiring Problems | Intermittent engine problems, flickering lights, no power to components, strange noises. | Damaged wires, corroded connections, loose connections, short circuits. |
Control Module Malfunction | Engine misfires, erratic performance, check engine light illuminated, difficulty starting. | Faulty module, software issues, or improper wiring to the module. |
Air Intake System Troubleshooting
The air intake system is critical for proper engine operation. It ensures a consistent and sufficient supply of air to the engine, which is directly related to the engine’s power output and efficiency. A malfunctioning air intake system can lead to various performance issues, from reduced power to complete engine failure. Understanding the workings of this system and how to diagnose common problems is crucial for maintaining optimal engine health.The air intake system comprises several components that work together to deliver air to the engine cylinders.
These components include the air filter, air intake hoses, and the throttle body. Issues with any of these components can disrupt the air flow and negatively impact engine performance. Efficient troubleshooting involves systematically identifying and addressing the source of the problem.
Air Filter Condition Check
Proper air filtration is essential for maintaining engine performance and longevity. A dirty air filter restricts airflow, leading to reduced power and increased fuel consumption. Regular inspection and replacement of the air filter are vital.
- Visual Inspection: Examine the air filter visually for signs of dirt, debris, or damage. A heavily soiled filter needs replacement immediately.
- Resistance Test: Use a simple resistance test to gauge the filter’s air flow restriction. A restricted filter will significantly impede air flow. A clean filter should allow easy airflow.
- Replacement Schedule: Refer to the vehicle’s owner’s manual for recommended air filter replacement intervals. Adhering to this schedule prevents significant performance degradation and potential engine damage.
Diagnosing Air Leaks
Air leaks in the air intake system can cause significant performance problems. Leaks in hoses or connections allow unfiltered air to enter the intake, resulting in reduced power and increased fuel consumption.
- Visual Inspection: Carefully examine all air intake hoses and connections for any signs of damage, cracks, or loose fittings. A leak might be visible as a noticeable air leak.
- Listening for Leaks: Use a stethoscope or your ear to listen for hissing sounds, which can indicate a leak. This method is particularly helpful in locating small leaks in hard-to-see areas.
- Pressure Test: Using a pressure gauge, apply pressure to the intake system while visually inspecting for leaks. A leak will cause a drop in pressure.
- Troubleshooting Methodology: When identifying the source of a leak, systematically check each component and connection. Begin at the air filter and proceed to the throttle body, ensuring all hoses are securely connected.
Transmission and Drivetrain Troubleshooting
Troubleshooting transmission and drivetrain issues can be a complex process, often requiring a systematic approach. Identifying the source of problems, whether related to fluid levels, unusual noises, or drive shaft malfunctions, is crucial for effective repair and preventing further damage. This section provides a guide to common issues and their diagnostic procedures.
Potential Transmission Problems
Various issues can affect the transmission, ranging from minor fluid leaks to complete component failures. These issues can manifest as shifting problems, rough operation, or complete loss of power. Proper diagnosis necessitates a thorough inspection of the transmission’s operation and components.
Checking Fluid Levels and Condition
Correct fluid levels and condition are vital for optimal transmission performance. Adequate lubrication prevents friction and wear, while proper viscosity ensures smooth operation. Insufficient fluid can lead to overheating and component damage, while excessive fluid can cause leaks and overflow issues.
- Fluid Level Check: Locate the dipstick and check the fluid level according to the vehicle’s specifications. Ensure the dipstick is clean before insertion and removal. Compare the observed fluid level to the manufacturer’s recommendations. Any discrepancies should be addressed.
- Fluid Condition Assessment: Inspect the fluid for color, odor, and consistency. Dark, burnt-smelling, or excessively thick fluid indicates a potential problem and requires further investigation. The presence of metal particles or debris suggests internal component damage. Refer to the vehicle’s manual for normal fluid characteristics.
Diagnosing Unusual Transmission Noises
Unusual noises emanating from the transmission can indicate various problems, from worn bearings to internal component damage. Systematic listening and analysis are crucial for pinpointing the source.
- Identifying the Noise: Carefully note the type of noise (e.g., grinding, clicking, whining, banging) and its location. A specific sound pattern may offer clues about the underlying issue.
- Analyzing Noise Characteristics: Observe how the noise changes with speed, acceleration, and gear selection. A noise that intensifies under load, for instance, could suggest a problem with the transmission’s clutch or bands.
- Correlation with Other Symptoms: Consider any other symptoms that may accompany the noise, such as shifting problems, loss of power, or vibrations. These factors help narrow down the possible causes.
Drive Shaft Troubleshooting
The drive shaft transmits power from the transmission to the wheels. Any issues with the drive shaft can result in drivability problems.
- Visual Inspection: Inspect the drive shaft for any visible damage, such as cracks, bends, or loose connections. Ensure all mounting bolts and clamps are secure.
- Checking for Excessive Play: With the vehicle supported safely, gently rotate the drive shaft to detect any excessive play or movement. Excessive movement may indicate a problem with the universal joints or other connections.
- Diagnosing Vibration: Vibrations in the vehicle, especially at higher speeds, may be a symptom of a damaged or misaligned drive shaft. Check for any visible misalignment of the drive shaft or any noticeable wear on the joints.
Engine Mechanical Troubleshooting: Engine Troubleshooting
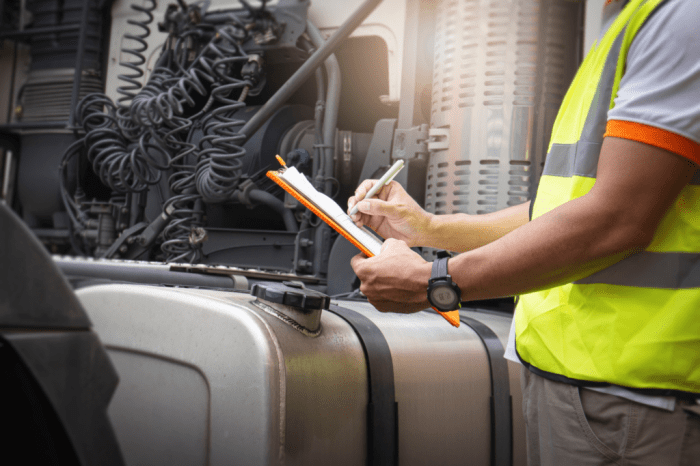
Engine mechanical issues can often be the most challenging to diagnose. Proper understanding of the engine’s internal components and the effects of wear and tear are crucial for accurate troubleshooting. Addressing these issues directly can often save significant repair costs and prevent more extensive damage.Mechanical failures, unlike electrical or fuel system problems, frequently manifest as gradual deterioration rather than sudden breakdowns.
This makes early detection and intervention critical to maintain optimal engine performance and longevity.
Importance of Proper Lubrication
Lubrication is fundamental to the smooth operation of any engine. Adequate lubrication reduces friction between moving parts, preventing excessive wear and tear. Insufficient lubrication can lead to seizing, scoring, and eventual catastrophic failure of components like the crankshaft and connecting rods. Proper oil viscosity, consistent oil changes, and a functioning oil system are essential for maintaining optimal lubrication.
Diagnosing Crankshaft and Connecting Rod Problems
The crankshaft and connecting rods are the heart of the engine’s power transmission. Issues with these components can manifest in several ways, including unusual noises (knocking, ticking, or grinding), loss of power, vibrations, or difficulty starting. Visual inspection of the crankshaft for cracks or excessive wear, along with careful examination of the connecting rods for bending or misalignment, are essential diagnostic steps.
A comprehensive analysis of the oil for metal particles can also indicate potential damage. Engine vibration analysis can provide insights into the health of the crankshaft and its bearings.
Identifying and Diagnosing Engine Block Problems
The engine block is the structural foundation of the engine. Problems with the engine block often lead to leaks, overheating, or significant performance issues. Visual inspection for cracks, warping, or distortion is paramount. Leaks can be identified by inspecting the block for oil, coolant, or other fluid leaks. Excessive vibration or unusual noises can indicate potential block damage.
Measuring block temperatures during operation can identify overheating issues.
Common Mechanical Engine Issues
- Crankshaft Bearings Failure: This can lead to severe knocking noises and eventually seizing of the engine. A common symptom is noticeable engine vibration, particularly at high speeds. Proper lubrication and regular maintenance are key preventative measures.
- Connecting Rod Problems: Bent or damaged connecting rods cause uneven power distribution and potentially lead to engine damage. A pronounced knocking sound, particularly when accelerating or under load, often indicates this problem. Checking for oil leaks around the connecting rod bearings is important.
- Piston Problems: Damaged pistons can cause uneven combustion and loss of power. Misfires, loss of power, and unusual noises are common symptoms. Regular inspection of the piston rings and cylinders for wear is vital.
- Cylinder Head Issues: Cracked or warped cylinder heads can lead to coolant leaks, loss of compression, and poor performance. Visual inspection for cracks or distortions is essential. Checking coolant levels regularly is also a crucial preventative measure.
- Valve Train Problems: Sticking or broken valves, damaged valve springs, or worn camshafts can cause knocking noises, rough idling, and loss of power. Listening for abnormal noises and inspecting the valve train components for wear is critical.
- Engine Block Cracks: Cracks in the engine block can lead to coolant leaks, loss of compression, and engine failure. Visual inspection and pressure tests are essential diagnostic tools.
- Oil Leaks: Oil leaks are frequently a symptom of damaged gaskets, seals, or bearings. Identifying the source of the leak and addressing the root cause is crucial.
Specialized Engine Troubleshooting
Troubleshooting specialized engines, such as diesel, hybrid, and turbocharged engines, requires a deeper understanding of their unique operational characteristics. These engines often utilize different components and systems compared to conventional gasoline engines, leading to specific troubleshooting procedures. Understanding these nuances is crucial for accurate diagnosis and efficient repairs.
Diesel Engine Troubleshooting
Diesel engines differ significantly from gasoline engines in their combustion process, fuel injection systems, and emission controls. Diagnosing issues often involves analyzing fuel injection timing, pressure, and quality. Diesel engines are prone to issues with injector wear, pump malfunctions, and clogged filters. Early detection and prompt action are crucial for minimizing potential damage.
- Fuel Injection System: Inspecting the fuel injectors for leaks, clogged nozzles, and proper injection timing is paramount. High-pressure fuel pumps and common rail systems require specialized tools and expertise.
- Compression Testing: Measuring compression pressure in each cylinder is critical for identifying potential piston ring wear or valve problems.
- Emission Controls: Diesel engines frequently use complex emission control systems, including particulate filters (DPFs) and exhaust gas recirculation (EGR). Problems with these components often manifest as performance issues or emissions failures.
Hybrid Engine Troubleshooting
Hybrid vehicles combine gasoline engines with electric motors and batteries. Troubleshooting hybrid systems requires understanding both the gasoline engine and the electrical components. Diagnosis often involves electrical system checks, battery condition assessments, and analysis of the powertrain control module (PCM).
- Battery Testing: Checking the battery’s state of charge, voltage, and capacity is essential. Problems with the battery can significantly impact the vehicle’s operation.
- Electrical System Analysis: Identifying faults in the electrical system is vital, encompassing the various sensors and actuators within the hybrid system.
- PCM Diagnostics: Utilizing specialized tools and software to read fault codes and data from the PCM is crucial for pinpointing the source of issues.
Turbocharged Engine Troubleshooting
Turbocharged engines often exhibit unique challenges due to the added complexity of the turbocharger and its interaction with the engine. Troubleshooting turbocharged engines frequently involves examining boost pressure, turbocharger bearings, and wastegates.
- Boost Pressure Monitoring: Precise measurement and analysis of boost pressure are vital for diagnosing turbocharger malfunctions or problems with the exhaust system.
- Turbocharger Inspection: Inspecting the turbocharger for wear, leaks, and damage is important for identifying potential issues.
- Wastegate Function: Assessing the wastegate’s function and its ability to regulate exhaust pressure is essential.
Older vs. Newer Engine Troubleshooting
Troubleshooting older engines often involves manual inspection and basic diagnostic tools, while newer engines rely heavily on electronic diagnostic tools and sophisticated sensor networks. Understanding the specific diagnostic methods used in each generation is crucial for accurate problem identification.
- Older Engines: Physical inspection of components, such as valves, gaskets, and hoses, often yields valuable insights. Basic diagnostic tools, like voltmeters and pressure gauges, are commonly used.
- Newer Engines: Advanced diagnostic tools and software provide detailed information about the engine’s operation. These tools allow for real-time data acquisition and analysis.
Variable Valve Timing Troubleshooting
Variable valve timing (VVT) systems enhance engine performance by adjusting valve timing dynamically. Troubleshooting VVT systems involves examining the actuators, sensors, and related control modules.
- Actuator Functionality: Ensuring proper operation of the VVT actuators is essential. Issues with the actuators can result in inconsistent valve timing and performance problems.
- Sensor Integrity: Assessing the accuracy of sensors that provide feedback to the control module about engine conditions is crucial. Malfunctioning sensors can lead to incorrect valve timing adjustments.
- Control Module Analysis: Diagnosing issues with the control module that manages the VVT system is essential. Problems with the control module can cause various performance and operational issues.
Closure
In conclusion, mastering engine troubleshooting is a valuable asset for any vehicle owner. By understanding the various components, their interactions, and the diagnostic methods, you can effectively address a wide array of issues. This comprehensive guide provides a solid foundation for tackling engine problems, saving you time and money.
FAQ Compilation
What are the most common causes of engine misfiring?
Misfiring can stem from various issues, including faulty spark plugs, ignition coils, fuel delivery problems, or even a problem with the air intake system. A thorough inspection of each component is crucial for diagnosis.
How do I check the engine oil level?
Locate the dipstick, wipe it clean, reinsert it, and remove it again. The oil level should be between the minimum and maximum marks on the dipstick.
What are the typical signs of a cooling system leak?
Look for puddles of coolant under the vehicle, a low coolant level, or a hissing sound from the cooling system components.
What are some basic tools needed for engine troubleshooting?
A multimeter, torque wrench, socket set, and various screwdrivers are essential for most engine diagnostics. Specific tools might be needed for certain systems or procedures.